Materials’ testing is the essence of an asset integrity approach.
It is the most essential testing regarding fit for service components, structures, products or product lines. All industries work on the principle that their equipment will perform to the end of its designed lifetime cycle with minimum service, under the properties the materials were chosen for. Material testing is, therefore, the only sensible approach for every industry that respects its infrastructure and equipment and desires optimum performance of an asset under continued production.
At ATOM DYNAMIC, thanks to our extensive experience in metallurgy science, along with replica metallographic testing, in lab-testing, conventional and advanced NDTs, we can understand and explain fatigue, corrosion, the creep phenomenon, or the hydrogen attack phenomenon.
Consequently we can provide solutions fit for service calculations, the measurement of the remaining life of the component, material failure analysis, asset integrity management and any other advices and studies imposed by a client’s needs.

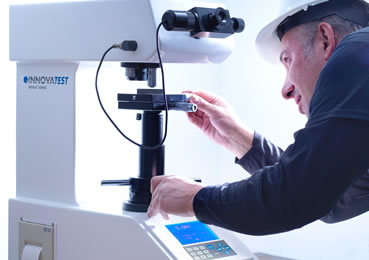
ATOM DYNAMIC offers NDE services of in-situ metallography which is considered important for assessing the health of the equipment that operates under different plant conditions.
The Oil, Gas and Energy industry needs safe, trouble free and productive operations, adopting a predictive maintenance approach. Critical operation components are subjected to a variety of hostile environments that necessitate microstructure assessment to monitor in-service degradation. Microstructure plays an important role in controlling properties such as Mechanical, Metallurgical, Physical properties and Corrosion of an alloy.
The service of in situ metallography we offer involves location selection, mechanical grinding & polishing / electrolytic polishing, electrolytic etching or chemical etching, replication and micro structural observation.
The principle deterioration mechanisms that can be detected by the use of in situ metallographic techniques are:
- Graphitisation
- Defradation of Pearlite
- Creep Damage
- Hydrogen Attack
- Thermal Fatigue
- High Temperature Oxidation
- Decarburisation
- Grain Coarsening
- Embrittlement and carburization
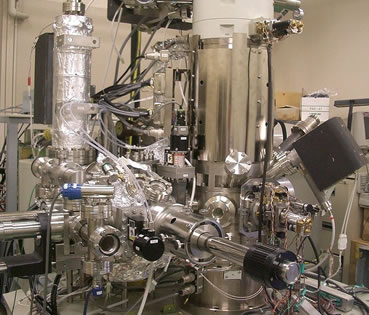
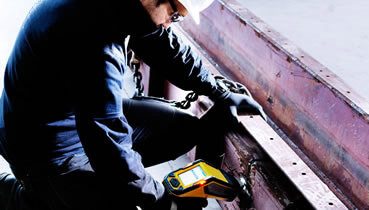
POSITIVE MATERIAL IDENTIFICATION (PMI)
The need to analyze and establish the chemical composition of a metallic alloy material or weld joint, by reading the quantities of the various elements in the product, is present now more than ever.
ATOM DYNAMIC offers this service with expert engineers and sophisticated portable XRF equipment.
HARDNESS TESTING
ATOM DYNAMIC offers hardness testing services through an extensive range of advanced portable hardness testers, such as portable rebound type, telebrineller (poldi) type and ultrasonic (UCI) type.
The different characteristics of the object to be examined define the choice of the instrument to be used.
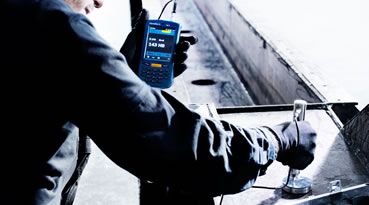
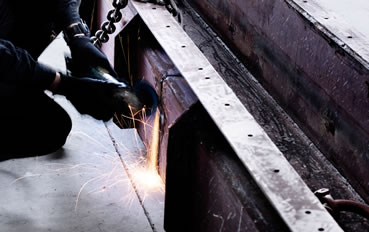
FERRITE TESTING
The need to define the amount of ferrite present in austenitic steels creates new requirements in the petrochemical industry.
ATOM DYNAMIC owns a variety of instruments, calibration blocks and experienced specialists to offer this service.