Atom Dynamic specializes in heat treatment services.
Our extensive know-how allows us to perform Heat Treatment activities on pressure vessels, welded constructions, piping and pipeline welded joints with the use of mobile electrical heating units, mobile induction units and thermal gas combustion equipment, both on new constructions as well as repairs, such as shutdowns or turn around projects.
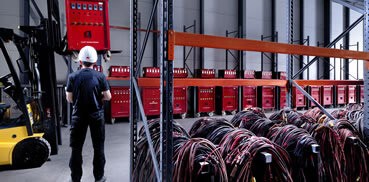
Atom Dynamic Heat Treatment services include the full spectrum of applications:
- Welding Preheat — Advanced automated systems control and document welding preheat to reduce thermal stress in three primary ways. They drive off moisture that would release hydrogen that could penetrate the steel and cause porosity and subsequent cracking and reduce heat loss in the surrounding metal, minimizing the rate of weld hardening and allowing hydrogen that is present to escape. The microstructure and durability of the heat-affected zone is improved.
- Post-weld Heat Treatment — Carefully controlled PWHT is a crucial step in maximizing the life of your process equipment. PWHT tempers the metal and reduces tensile stresses, minimizing the risk of brittle fracture, stress and corrosion cracking and metal fatigue. Our engineers ensure the structural integrity of the vessel or unit during treatment while our advanced PLC-controlled unit achieves the precise control needed to get the maximum benefit from the treatment.
- Line Thawing — ATOM DYNAMIC can deploy electrical and induction resistance heating that gets frozen lines flowing again quickly and keeps them flowing until your plant’s steam-tracing system is working again.
- Hydrogen Removal — We can improve the integrity of welded components and minimize the risk of fabrication-related cracking. Used prior to cutting or welding older process equipment, heat treatment application can help protect equipment during cutting and welding as well as improve the quality of the finished work.
- Heat Treatment (Annealing and Normalizing) — We offer a range of services for annealing and normalizing to alter the properties of metals that may or may not contain welds
Our high-quality services in the field of heat treatment are based on 30 years of experience in engaging with demanding customers; our services have been endorsed by a number of industries including power stations, refineries, petrochemical plants, metal fabrication shops and marine.
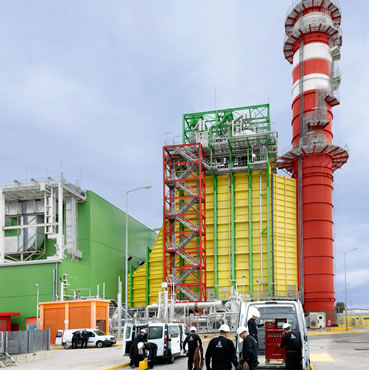
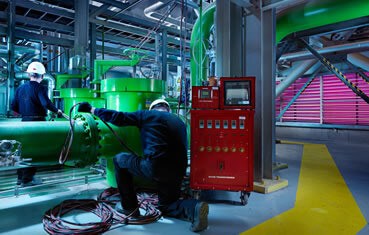
The traditional low-voltage Electrical Resistance method of heat treating uses ceramic blankets stepped down to 30 or 60 volts to provide a quick and convenient approach to many jobs, particularly preheat and PWHT.
The well-maintained, properly calibrated, high-efficiency equipment we use allows us to engage on any heat treatment application and offer high-quality services ensuring constant control and monitoring over the process.
Our expertise in electrical resistance H.T. covers an asset’s entire lifecycle -from research and construction to production and operation- while our services and solutions ensure quality control, safe operation and production, aiming to extend an asset’s lifecycle.
We help customers optimize their efficiency, reduce costs and maximize performance while minimizing operational and regulatory hazards through our well-designed and executed PWHT Project Management.
Our worldwide reputation in the field and the values governing our operations, such as top quality and safety of services, along with our commitment to delivering under highly exacting circumstances, have made us an indispensable, preferred partner of a large number of demanding customers in Heat Treatment Services.
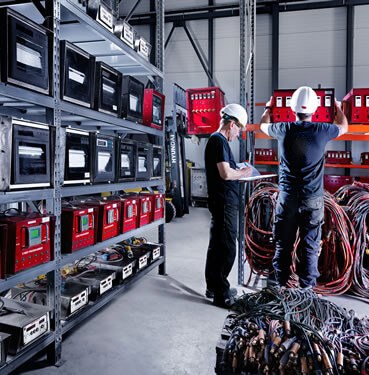
eMachine
ATOM DYNAMIC’s management approach on Heat Treatment ensures the excellence of our performance by incorporating the most advanced technologies in communications and software solutions.
Ensuring optimum quality control by real-time data-collection in our Heat Treatment service -including the process parameters themselves, as well as the activities on the application field- this management approach to operation addresses the most demanding requirements of the Oil and Gas industry.
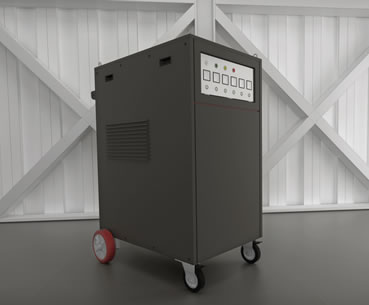
With the use of eMachine, ATOM DYNAMIC alone is in position to:
- Reduce a customer’s safety hazards, operational cost and administrative burden
- Allow centralized monitoring and quality control of the Heat Treatment works by the customer’s Quality Control Team
- Allow customers to monitor all phases of the process and the works associated with it
- Utilize and dramatically improve the time required to complete a project
- Address the Heat Treatment process with the highest quality standards in a more flexible and cost-effective way