The main advantages of induction heating are:
- Optimized Consistency: Induction heating eliminates the inconsistencies and quality issues associated with open flame, torch heating and other methods.
- Maximized Productivity: Production rates can be maximized because induction works so quickly; heat is developed directly and instantly inside the part. Startup is virtually instantaneous.
- Improved Product Quality: With induction, the part to be heated never comes into direct contact with a flame or other heating element.
- Extended Fixture Life: Induction heating rapidly delivers site-specific heat to very small areas of your part, without heating any surrounding parts.
- Environmentally Sound: Induction heating systems do not burn traditional fossil fuels; induction is a clean, non-polluting process which helps protect the environment.
- Reduced Energy Consumption: 90% of the energy used for the process is reduced compared to conventional electric heat treatment.
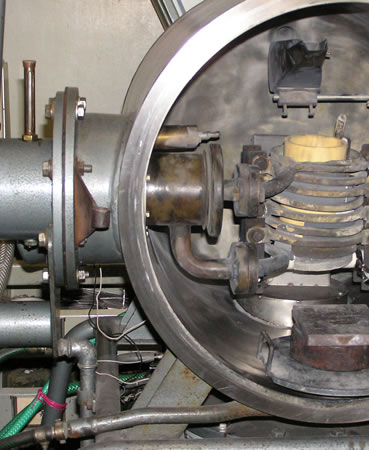
We offer a wide range of induction-heating applications delivering high quality, efficient services:
- Welding Preheat — Advanced automated systems control and document welding preheat to reduce thermal stress in three primary ways. WP drives off moisture that would release hydrogen that could penetrate the steel and cause porosity and subsequent cracking and reduces heat loss to the surrounding metal, minimizing the rate of weld hardening and allowing hydrogen that is present to escape. The microstructure and durability of the heat-affected zone is improved.
- Post-weld Heat Treatment — Carefully controlled PWHT is a crucial step in maximizing the life of your process equipment. PWHT tempers the metal and reduces tensile stresses, minimizing the risk of brittle fracture, stress and corrosion cracking and metal fatigue. Our engineers ensure the structural integrity of the vessel or unit during treatment and our company’s advanced PLC controlled unit achieve the precise control needed to get the maximum benefit from the treatment.
- Improved Product Quality: With induction, the part to be heated never comes into direct contact with a flame or other heating element.
- Coating Removal — We can improve the integrity of welded components and minimize the risk of fabrication-related cracking. Used prior to cutting or welding older process equipment, heat treatment application can help protect equipment during cutting and welding as well as improve the quality of the finished work.
- Heat Treatment (Annealing and Normalizing) — We offer a range of services for annealing and normalizing to alter the properties of metals that may or may not contain welds.